Less of this.
June 15th, 2018
“People show up for the meetup but come back for the people.”
— Scott Heiferman, Meetup
Organizers Develop Leaders
June 14th, 2018
Marshall Ganz discusses leadership and what it means to be an organizer. Ganz is a Senior Lecturer at the Harvard Kennedy School.
He says:
“Organizers think of themselves as people that develop the leadership of others.”
And that:
“Leadership [is] accepting responsibility for enabling others to achieve purpose under conditions of uncertainty.”
Finally:
“If everything is working the way it’s supposed to and all the systems are go, what do you need leadership for? Leadership is about dealing with challenge, contradiction, the unexpected, and the novel.”
ORID: Conversation Flow 101
June 13th, 2018
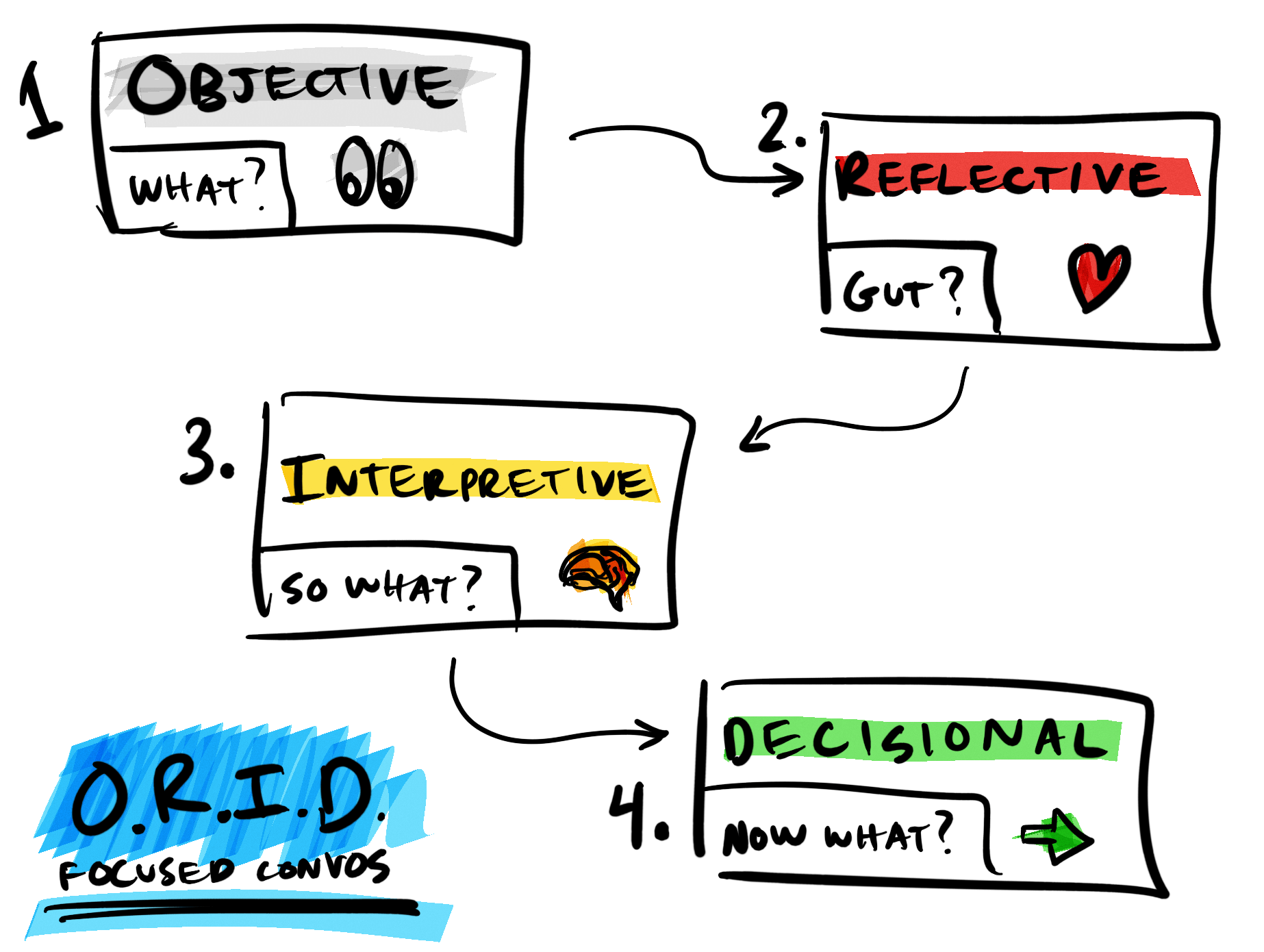
ORID (Focused Conversation)
I think about this whenever prepping for research interviews. I’m trying to gauge if our sequence of questions “feels” right.
Does the order seem natural? Do we avoid coming on too strong? Are we building up to the meaty stuff?
Today I learned about the Focused Conversation method—also called the ORID method—at a Facilitation Fundamentals course by The Design Gym. (They adapted the content from The Institute of Cultural Affairs).
ORID is a framework to logically progress through four different levels of thinking: Objective, Reflective, Interpretive, Decisional.
For me it’s conversation flow 101. A helpful starter guide to structure any discussion, interview, survey, or even informal chat. A roadmap for progressing through topics.
- (O) Objective – Facts, data, info
e.g. What happened? What are the facts? - (R) Reflective – Feelings, reactions, responses
e.g. What was challenging? What surprises you? - (I) Interpretive – Meaning, significance, implications
e.g. What’s really being said? What are the root causes? Pros/cons? - (D) Decisional – Summary, decisions, actions
e.g. Next steps? Key takeaways? Where do we agree?
Bonus: a fun way to remember ORID is…
- What?
- Gut?
- So what?
- Now what?
Thanks to The Design Gym for a great day and plenty of brain food. I recommend their Facilitation Fundamentals course!
Right Support, Right Time
June 12th, 2018
I helped interview Ru Hill who runs Surf Simply, a surf coaching resort in Costa Rica. I’ve been thinking about that chat from a few weeks ago.
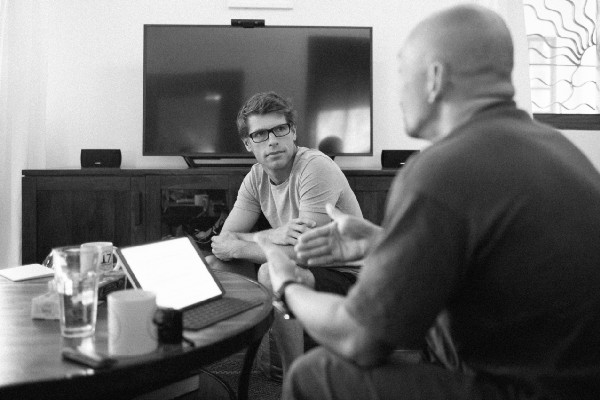
Kai chatting with Ru about building Surf Simply
One of the most impressive things he and his team have done is outline a surfing “Tree of Knowledge.” It’s a flowchart that visualizes key surf skills and their dependencies.
It allows beginners to clearly see a road map telling them which skills need to be mastered first, what they will lead on to and, most importantly, why. For more experienced surfers, the poster tells you what you should be aiming for next and what gaps in your knowledge might need to be revisited in order for you to progress
This Tree of Knowledge reminds me how it’s most helpful to deliver people the right support at the right time. It’s tempting to shower someone in resources, training, and knowledge.
But a real process person thinks, what do you need right now to get where you want to go?
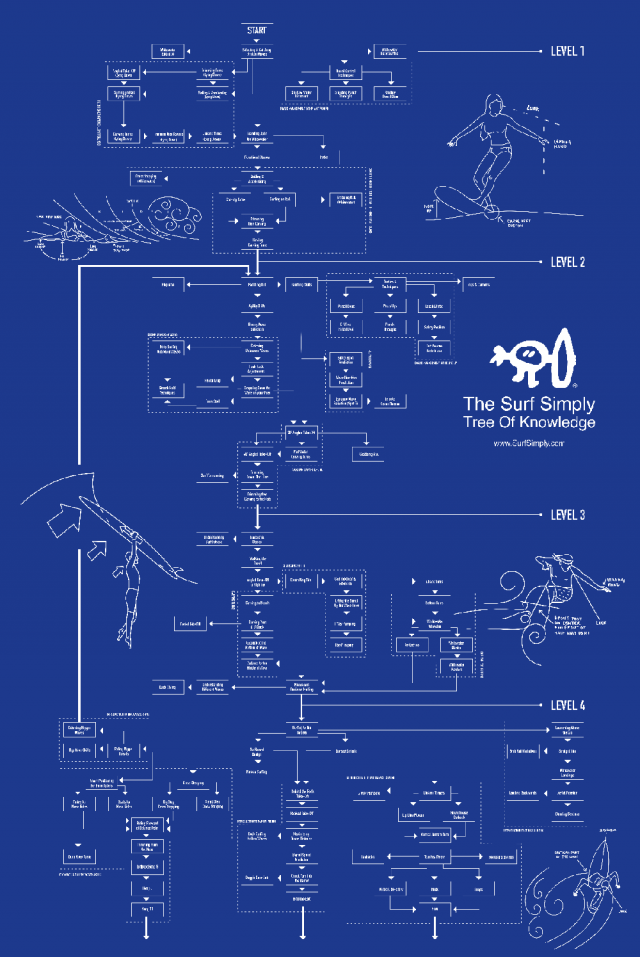
The Surf Simply Tree Of Knowledge
Who and Why
June 11th, 2018
Lately, I appreciate getting clarity on the Who and Why before What, How, When, and Where.
Whether I’m writing an essay or hosting a dinner, knowing Who and Why make other decisions easier.
- Who am I hoping to serve/reach/help? → audience!
- Why am I doing this? → goals!
Value vs Non-Value Added Activities
June 10th, 2018
I wrote a (short) autobiography when I was in 5th grade. My concluding sentence was:
“It’s better to be busy than to be bored—to live a full life than an empty one.”
I’m not sure if I agree with 10-year-old Kevin. Depending on the process, I’d gladly cut certain activities in exchange for the boredom.
Any process can be thought of as performing activities with inputs in order to produce outputs.
We hopefully create value through those activities. And Lean Thinking distinguishes which activities are “value added” versus “non-value added.”
If we’re making a pizza, sprinkling delicious cheese is value-added. Letting the oven pre-heat might be non-value added, but “necessary waste.” However, waiting for the oven to free up or fixing a botched sauce are non-value-added activities — “pure waste.”
We should aim to emphasize value-added activities, minimize necessary waste, and eliminate pure waste.
That said, classifying activities can be easier said than done. First, value must be clearly defined (Value = delicious pizza? What does delicious mean? For whom?). Second, categorization should go beyond intuition. Use data. Observe the process. Gather perspectives.
Mm… Pizza. 🍕
6S, How to Make Any Space People-Friendly and Efficient
June 9th, 2018
Lean is a “journey” not a “state.”
— Earll Murman, Lean Advancement Initiative (LAI)
My parents are professional process people.
Dad leads manufacturing for hardware startups—currently for a smart baby-monitor. Mom runs infection control at hospitals—designing processes to reduce infection risks for both patients and staff.
Perhaps that’s why I’ve always gravitated towards process heavy projects and tasks. It’s in my blood!
How can process support people power?
I’ve decided to embrace my proclivity for process.
Specifically, I want to learn more about how explicit processes help big groups of people work effectively and do ambitious things. How do we design structure with both empathy and efficiency in mind?
Step one: learn about established tools and vocabulary from the world of “process.” So, two weeks ago I began working through this MIT open online course on Lean Thinking, a methodology for continuous process improvement.
Lean thinking and 6S
The central idea of lean is to create value and eliminate waste. But my favorite description of Lean Thinking from the class is:
“A focused application of common sense.”
One simple lean tool is called 6S (there are variations with different quantities of S). I see it as a mnemonic for effectively organizing anything—an activity, workspace, or resource.
In other words, 6S reminds us how to make a space people-friendly and efficient.
Here’s how I summarize 6S with actionable questions:
- Sort – How do we get rid of unnecessary items?
- Safe – How do we remove the risk of dangerous mistakes?
- Straighten – How do we better organize or arrange items?
- Scrub – How do we keep our space consistently clean?
- Standardize – How do we establish helpful models, guidelines or procedures?
- Sustain – How do we keep this all up?

6S applied to a surgical tray. (Introduction to Lean Six Sigma Methods, MIT Opencourseware)
Imagine applying 6S to a resource portal, training, shared space, or communication channel. What are all of the ways we can improve the use of and interactions around that space?
I love frameworks like this. They help me build on intuition. To look at a problem from more angles more quickly. Watch out, world. I’m going to 6S everything.
P.S. Thanks to MIT and LAI for making this course and all of the materials available! I love this stuff.